Statistical process control
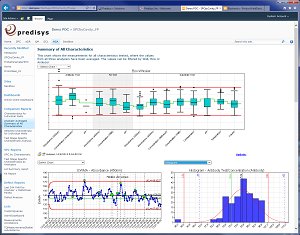
Online statistical process control
However, in addition to a comprehensive set of control charts and statistical tools for statistical process control (SPC) and advanced statistical analysis, today's focus is increasingly on additional benefits for users, system managers and ÍT departments.
Unlike traditional SPC software applications used offline on a desktop pc, modern rich web application is required for internet generation. Robust server-based solutions provide centralized data storage and a scalable architecture that allows our customers to add additional applications and processing power based on their business needs. This architecture increases flexibility, significantly lowers total cost of ownership, and provides the most intuitive and user-friendly system on the market today.
Success factors for SPC
- Data sources for the SPC system can be highly diverse; some can be taken directly from a measurement system if the interfaces are available. Other sources are order-related data, which are available in SAP or another ERP system. Up to so called flat files like .csv or Excel files. Some data is entered manually and must also be able to be entered manually - which not all software systems can handle. These different data sources must be merged and consolidated.
- The numbering systems to correctly assign products, intermediates and raw materials are often not in place. Standardization, especially across different plants, can be very costly.
- The quality of the measurement data is often questionable. It is not recorded with which measuring system is measured. Does this system have a measuring system analysis? It is rarely recorded which operator (anonymously if necessary) has carried out a work step.
- Often, "only" those product characteristics are recorded for which a specification is also available. Unfortunately, the process parameters that are necessary for learning why a particular defect occurs are not recorded.
- The software must not have too long response times. After entering a value, the updated graphic (control chart) must be immediately visible on all screens that are currently displaying this parameter. This point alone often makes working with offline solutions (Excel) impossible.
- If a value occurs outside the control limits, actions must be stored (OCAP - Out of Control Action Plan). Defining and following these actions helps a lot to systematize the workflows. However, it also produces a lot of work in the start-up phase of such an SPC system. The executed actions must be stored in the database and must also be recognizable when the control chart is called up later. This means that a point can be clicked from the graphic and information can be entered for this point. This information must be transferred directly from the graphic to the database.
- A wide variety of limit values and characteristic values must be available in the database. Only in comparison to these values data can be interpreted correctly: Plausibility limits (for the first quick check of data received from the database. Specification limits (often customer or order related) Intervention limits (are often adjusted in time and must be traceable retroactively) Warning limits (are no longer included in the newer editions of standards, but can make sense in some cases) Target values (often customer or order related) Standard deviations (Short Term and LongTerm) If these data are not available or must be obtained with effort, an SPC system will not work well.
Requirements for an SPC system
- Multiple data sources and formats
- Manual data entry
- Semi-automatic data transfer
- Fully automatic data transfer
- Simple and intuitive interface
- Graphical user interface
- Visual and audible alarm
- Monitor and control the process