Quality management
Statistical quality assurance or quality control, or SPC for short, comprises various methods for ensuring specified quality requirements.
In our training courses, you will learn how to improve processes continuously and avoid errors instead of correcting errors after the fact. At STATCON, quality assurance is not reduced to the consideration of control charts, but is embedded in the broader area of reliability, measurement system and process capability analysis.
Building on basic procedures for control charts (-, s, R-, MA-, CUSUM charts), we provide you with application-ready knowledge in more advanced procedures such as measurement system analysis (MSA, Gage R&R, Precision To Tolerance) and show you how to integrate these procedures into your processes. STATCON training courses are never based on a standardized approach.
Our competent and experienced trainers address your individual requirements and thus ensure the practical applicability of the imparted training content in your company.
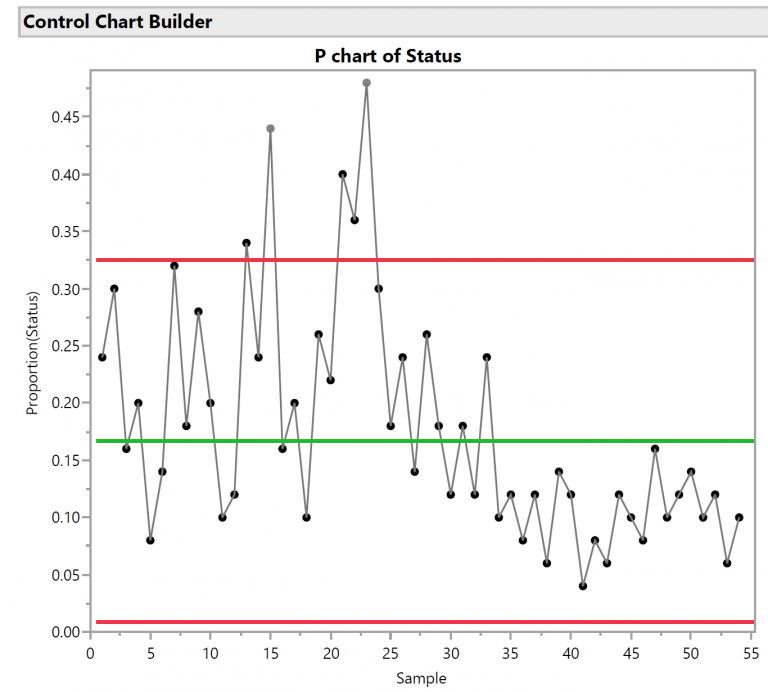
The term statistical quality assurance refers to statistical methods used in the industrial manufacturing of products and/or for the definition and optimization of processes.
Some of these methods follow a standardization, others are defined industry-specific.
This area includes, among others, the topics
Measurement system analysis
Within the scope of the measurement system analysis, the scatter of measurement systems is investigated. Different situations have to be differentiated:
- Determination of the inherent scatter of a measuring system
In this area, procedures 1 and 4 of the Measurement System Analysis (MSA) and the GUM (Guideline for the Uncertainty of Measurements) should be mentioned. - Determination of the scatter of a measuring system in the application
Type 2 and 6 of the MSA as well as DIN 72514 - Comparison of the quality of measurement system
Ringversuche (DIN 5725)
SPC was developed by Walter A. Shewhart and first published in 1931. In this respect, the methodology can certainly not be described as new from today's perspective.
The basic idea is that the quality of a product is essentially determined by the combination of the individual parts and thus depends on the scatter of the parameters of these individual parts. This scatter can be due to two fundamentally different causes:
- random deviations from the nominal value (often mean value)
- special causes (man, machine, material, method, construction, ...)
Process control / Process control (SPC)
Quality control charts have been developed to differentiate between these two causes. If a process change is necessary, it is highly likely that one of the special causes should provide the rationale. The method is used very often in Six Sigma projects. Process monitoring software can be divided into two groups:
Offline
First, data is collected over a period of time and evaluated once at the end of this period. The period can be defined very flexible (shift, day, week, lot, batch, ...).
Online
Hardware and software together make it possible to be informed immediately and automatically about the current values of quality parameters.
Process capability
The capability of a process is measured by whether the process produces characteristic values that are within the given limits (specifications).
Even if all characteristic values are within the limits (good process or after sorting), a probability can be calculated on the basis of the scatter of the characteristic values that characteristic values may occur outside the limits.
The basic prerequisite for a long-term customer-to-supplier relationship is process stability (demonstrated by a control chart).
In case of a short-term relationship between customer and supplier (e.g. one-time delivery), the method without prerequisite is used as evidence.
The most important prerequisite for the applicability of the method is the knowledge of the distribution of the characteristic values. In most cases, the Gaussian normal distribution is assumed. The calculation methods are defined in ISO standard 21747.
Process capability analyses usually take place at discrete time intervals, so they can be called "offline". Online systems naturally provide the same information.
Sampling systems
Sampling systems are often used in incoming and outgoing goods inspection. There are a few different standards in this area:
- DIN ISO 2859 attributive test
- DIN ISO 3951 measuring test